

Good Manufacturing Practice: Guidelines for good manufacturing practice
- Materials and articles that come into contact with medicinal products, food and feed must not pose a health risk to consumers.
- Good Manufacturing Practice guidelines require manufacturers of such materials to optimize their entire process chain for maximum safety.GMP therefore plays a central role in production, both for the substrates used and for printing inks.
When quality deviations occur in the composition of pharmaceuticals, cosmetics, food and feed, this usually means negative health consequences for consumers. Good Manufacturing Practice (GMP) therefore provides comprehensive quality assurance guidelines to prevent such cases.
Since packaging and other contact materials can cause quality deviations, they are also included by GMP. The control of production processes and environments as well as the materials used are intended to ensure quality and safety for consumers.
WHAT IS BEHIND GMP?
In the case of pharmaceuticals and other products, deviations in quality can cause serious damage to the health of consumers. The reasons for such quality deviations can lie along the entire production process. To ensure that manufacturers take all necessary measures to exclude such risks, the guidelines on Good Manufacturing Practice exist in addition to the legal regulations.
WHERE DOES GMP ORIGINALLY COME FROM?
The reason for the development of GMP specifications were recurring cases in which medicinal products did not improve health, but on the contrary caused damage to health and even death. In addition to national legal regulations, the World Health Organization (WHO) provided the first GMP guidelines in 1968.
The EU GMP guidelines have been in force in Europe since 2006. They are divided into three areas:
- Part I contains basic requirements that must be observed around the manufacture of medicinal products.
- Part II sets out requirements for good manufacturing practice for active pharmaceutical ingredients.
- Part III additionally lists the necessary documents that are relevant for GMP (for example, quality risk management or the pharmaceutical quality assurance system).
GOALS OF THE GMP GUIDELINES
Just like drug safety legislation, GMP guidelines are designed to ensure the safety, efficacy and consistency of medicines. However, this applies equally to all materials that come into contact with medicines and food.
with regard to the placing on the market in the Community of materials and articles
intended to come into contact, directly or indirectly, with food,
while providing the basis for a high level of protection of human health and consumer interests."
(Regulation (EC) No. 1935/2004, Article 1)
In order to take into account as many causes of quality deviation as possible, Regulation EC No. 1935/2004, which was written for this purpose, also covers materials and articles that come into contact with food in any form.
To this end, Article 2 of the Regulation explains, among other things, the concepts of
- Active food contact materials and articles intended to extend shelf life or maintain condition, and
- smart food contact materials and items used to monitor the condition of packaged goods.
IS GMP INTERNATIONALLY UNIFORM OR ARE THERE DIFFERENCES IN INTERPRETATION?
Since Good Manufacturing Practice is incorporated into national legislation, it is handled with corresponding differences. In Germany, for example, GMP is part of the Pharmaceuticals and Active Ingredients Manufacturing Ordinance, while in the USA the guidelines of Current Good Manufacturing Practice (cGMP) apply.
Apart from these, there are other international standards that deal with GMP. For example, for primary packaging materials for pharmaceuticals, ISO 15378 (which in turn refers to ISO 9001) and for cosmetics, ISO 22716.
To this end, various industries are developing special GMP guidelines with more specialized specifications, such as the European Carton Makers Association (ECMA) for European folding carton manufacturers or the European Printing Ink Association (EuPIA) for printing ink production.
WHAT APPLICATION AREAS DOES GMP COVER?
The GMP guidelines alone do not constitute a quality assurance system. However, they do provide the tools for comprehensive quality assurance management. This covers different areas of application, from personnel to premises and hygiene to testing and documentation:
- The personnel must be available in sufficient numbers and have the necessary training. This also includes regular training and education as well as clearly defined responsibilities.
- The premises must be suitable for the respective purpose (production, testing and storage). An appropriate size, sufficient access and adequate cleaning must be demonstrated (in the form of a qualification) for this purpose.
- The same applies to the equipment (i.e. devices and the like), the proper functioning of which must be ensured for the entire duration of use. Evidence of this must also be provided.
- Hygiene covers various areas, from the behavior of personnel and the wearing of protective clothing to regular cleaning, disinfection and waste disposal. Hygiene and safety officers are responsible for ensuring compliance with hygiene requirements.
- The documentation should be standardized and comprehensible and suitable for the respective mapped company areas (production, cleaning, etc.). The documents must ensure the control of changes and deviations.
- The validation of processes and methods is intended to prove that they are carried out according to plan, within set criteria and reproducibly - and deliver a product that meets the given specifications.
- Change control must be able to distinguish precisely between planned and unplanned changes, as well as between critical (if product quality is affected, for example) and non-critical changes. The same applies to deviation control.
Companies must also ensure appropriate risk management and conduct regular internal audits.
WHY IS GMP IMPORTANT FOR THE PACKAGING AND PRINTING INDUSTRY?
The keyword in this context is: migration risk. If packaging materials or printing inks come into contact with food, it must be ensured within the process chain for production that the quality of the packaged products is not impaired. Plastic, paper, cardboard or rubber must not cause any health hazards for consumers.
"COMMODITIES" WITH FOOD CONTACT
The Food and Feed Code (Lebensmittel- und Futtermittelgesetzbuch, LFGB) stipulates that the transfer of substances from "consumer goods" that could endanger human health or the quality of products is prohibited. In general, it is prohibited to manufacture, market or use consumer goods that are harmful to health.
In addition to coated cooking pots and plastic cutlery, consumer goods that come into contact with food also include packaging made of plastic, paper or cardboard. Added to this are the colors used in the design and production of the packaging.
However, the Federal Institute for Risk Assessment (BfR) emphasizes that there are no approval regulations for the articles and materials as such. The legal regulations only cover approval for individual materials used in manufacture.
The BfR recommendations cover various types of material:
- Paper, cardboard and paperboard for food contact (food packaging, kitchen towels, napkins, etc.)
- Cooking and hot filter papers (coffee filters, tea or cooking bags, etc.)
- Papers, cartons and cardboards for baking purposes (baking papers etc.)
- Absorbent pads based on cellulose fibers for food packaging
To this end, the BfR also deals with plastics, silicones and natural and synthetic rubber. Although the institute's recommendations are not legal standards, they are based on the current scientific and technical status required for health safety in accordance with the LFGB and Regulation (EC) No. 1935/2004.
However, in EU law, Regulation (EC) No. 2023/2006 regulates how materials and articles (including combinations of different materials for common use) should be handled in terms of GMP.
SAFETY FOR FOOD PACKAGING
The guide from the industry organization ECMA not only addresses all the core areas of Good Manufacturing Practice, but also provides guidance on the use of printing inks and coatings. They are critical when it comes to food safety - all the more so as the inks and coatings are used in various ways for paper and board packaging..png)
Manufacturers must take details into account, such as the use of UV printing inks. This is because these react with some paper or cardboard substrates when they are cured by UV irradiation. The resulting odor can cause packaged food to spoil. Under certain circumstances, special low-migration UV coatings may be used.
Paper and cardboard in particular are sometimes quite sensitive substrates. They absorb volatile materials from the ambient air, as well as vapors or liquids.
In order to produce safe packaging within the framework of GMP, all work areas must therefore be designed in accordance with the specifications. The selection of materials and printing inks suitable for the respective product play just as important a role as hygienic production or the avoidance of contamination during all supply routes. Complete documentation serves as comprehensive proof of quality.
At Labelprint24 we are well aware of our responsibility towards our customers and the end consumers. That is why we work completely in accordance with the requirements of GMP in our process chains and thus ensure the safety of the packaging, the packaged goods and the people who come into contact with them at all levels.
These articles may also interest you:
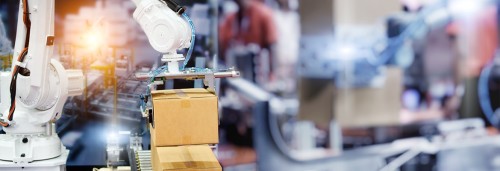
Packaging and logistics: Innovative concepts for the future
It goes without saying that logistics companies must also adapt to digitization and Industry 4.0. Yet these terms only very roughly describe the range of social, economic and technological trends that will become relevant in the near future - if they are not already.
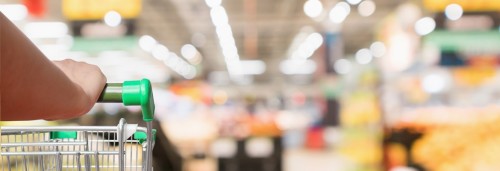
Consumer monitoring: What do consumers expect from packaging?
Consumers are becoming more reflective of their consumption behavior, which is why the type of packaging and its properties are playing an increasingly important role in their purchasing decisions. Above all, customers are demanding more sustainability in all areas of consumption.
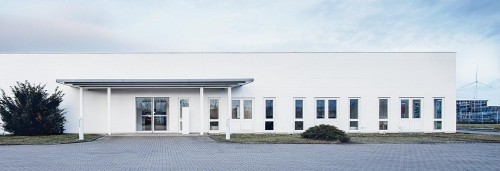
Zeithain prints labels for half of Europe
This is supposed to be a print shop? There's not a trace of printer's ink. Instead, spotless white rolls of paper are stacked in rows, and a cleaning machine rolls almost silently across the bare plastic floor. Half a dozen employees disappear between cuboid machines that, despite their size, only emit a half-loud click and hum.