

Finishes that leave
There are two main reasons to justify the cost of additional finishing of packaging materials after printing. The first reason is the need for additional protection of the surface of the packaging from external influences. These include rain, sunlight or mechanical abrasion. Typical finishes to create this protective layer are lamination or full-surface varnishing.
In addition, finishes should enhance packaging emotionally, they should appeal to the customer's "senses" and, in the best case, stimulate him to react. This can be a spontaneous purchase or the retention of a "formative" impression.
Discover our full range of labels and folding boxes now!
The queen of finishing - embossing
Our sense of touch is the basis of the so-called haptic effect. Alongside sight, hearing, smell and taste, this tactile perception is the most powerful of our senses. A haptic and visually appealing effect on printed matter is created by embossing, which is why embossing is also called the queen of finishes.
Definition imprinting:
"Embossing is the partial or planar profile-like forming of a material surface under the influence of pressure, temperature and time."
The mother of all embossing - blind embossing
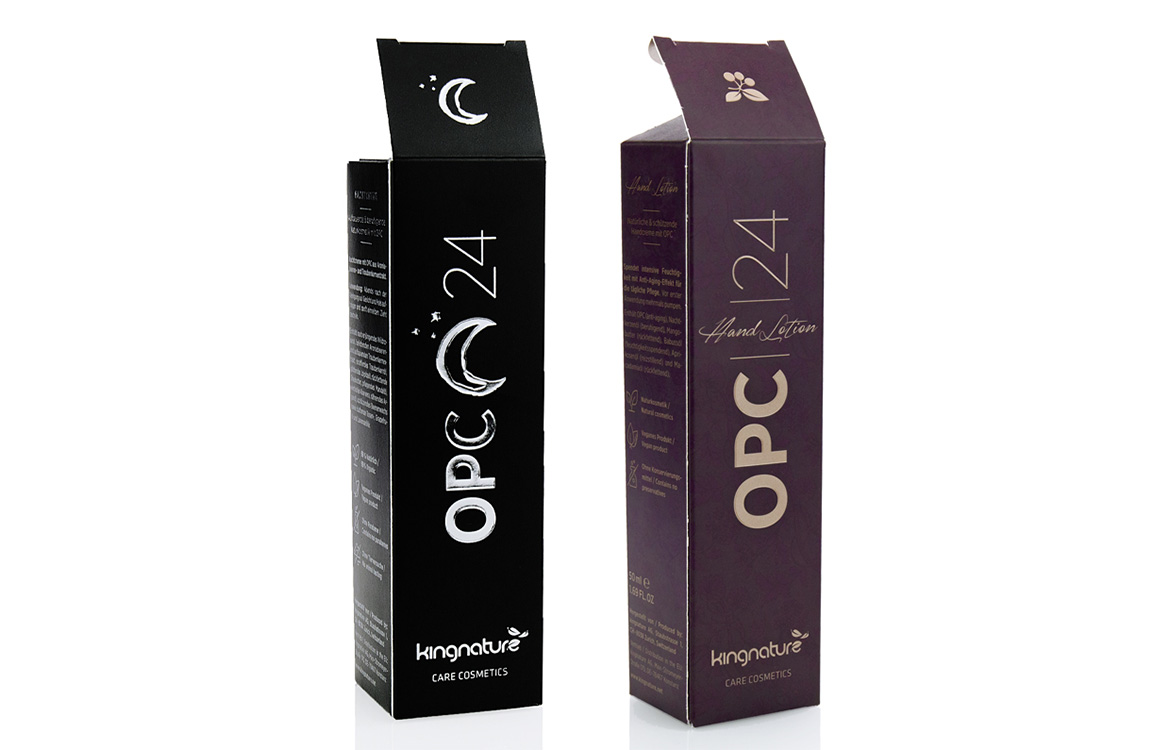
Blind embossing is a very old technique for finishing printed matter; it is the "mother of all embossing," so to speak. Coptic book covers were already blind embossed in late antiquity. Until today, blind embossing has also been used for finishing business cards, stationery, folding boxes and certificates.
In blind embossing, either a raised (high embossing) or deepening (deep embossing) deformation is achieved in the printing stock (paper, cardboard, carton) with the aid of an embossing die and under high pressure. Neither inks nor foils are used in this process. For this reason, blind embossing is also known as colorless embossing. Voluminous substrates are more suitable for blind embossing than thin paper.
The one-sided embossing - the plan embossing
Blind embossing can be performed as face embossing or relief embossing. In the case of plane embossing, there is only a compression of the material at the embossing point, which is created with the aid of a tool. The most distinctive feature of plane embossing is that only one side is embossed. The reverse side remains flat. Flat embossing can be performed without material application as blind embossing or with material application, e.g. as hot foil embossing.
The three-dimensional embossing - the relief embossing
Relief embossing requires two tools, the male and female dies. The dies press on the substrate from both sides to deform it three-dimensionally. Relief embossing produces very eye-catching finishes with striking visual and tactile effects.
Structure embossing is a special form of relief embossing. Texture embossing is the transfer of an embossing foil by means of pressure and heat to the material to be finished with simultaneous deformation of the substrate. The substrate is given a "structure" on the surface. This requires an embossing die with a suitable counter die and a hot stamping foil.
Even Braille, which is tactile for the blind and visually impaired - everyone knows the tactile dots on medicine packages - is either relief embossed or applied using digital embossing.
The hot foil stamping
Hot foil stamping is the transfer of stamping foils to the material to be finished by means of pressure and heat, without deforming the substrate in the process. This requires an embossing die and a special hot stamping foil. Hot stamping foils are available in various designs as gold, silver or colored foils, but effect foils or hologram foils are also available. Embossing foils best consist of several layers, a transfer layer and an adhesive layer. With digital hot foil stamping, an embossing tool is no longer required.
The cold foil stamping
Cold foil stamping is a process in which an embossing foil is applied to the substrate before printing. Unlike hot foil stamping, this does not require high temperatures or stamping tools. With cold foil stamping, the foil can usually be printed "inline", i.e. directly after application in the press. The visual effect of cold foiling is similar to that of hot stamping foils. Starting with just one standard silver foil, almost any color tone can be produced by printing over it in color. Even iridescent and reflective surfaces - such as metal, water or glass - can be realized realistically. Very fine structures and elements, such as fonts, lines and grids, can be represented with cold foil.
The microembossing
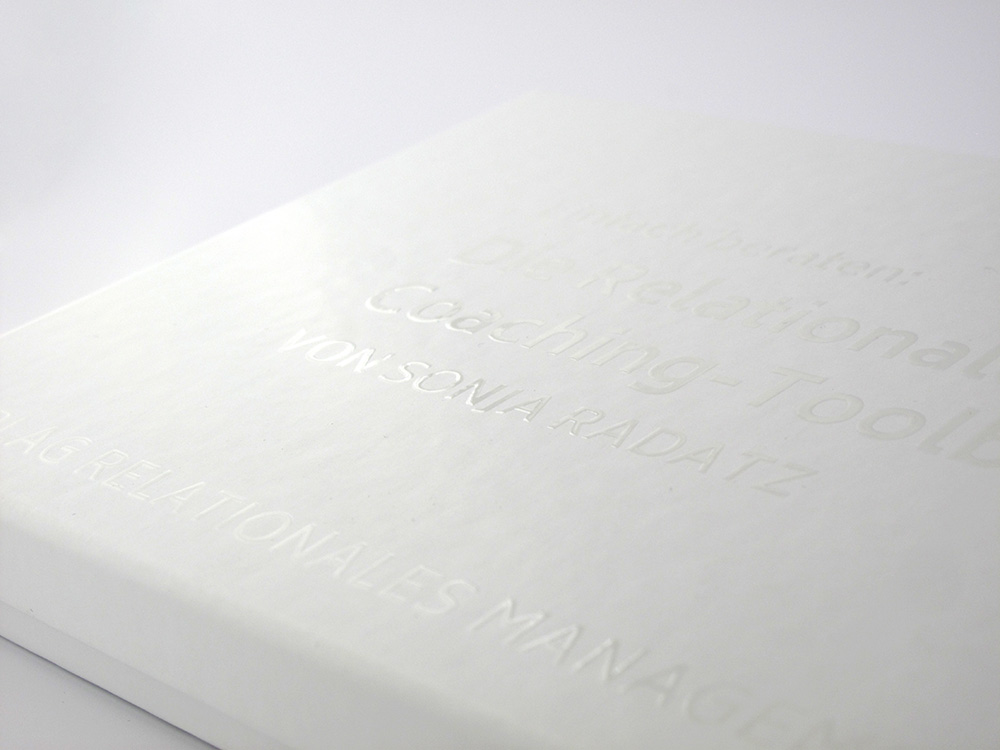
If the embossing foil is also to be embossed with the finest structures and the embossing die has fine structures, often created with a laser, this is called microembossing. This process is located between plano and structure embossing and is carried out using hot foil stamping. The cardboard or paper itself is not deformed.
The digital embossing
Digital embossing is a multiple application of ink or varnish to one and the same spot. The result then looks like an embossing. Individual colors or transparent dots of varnish are printed up to 50 times on top of each other. This process is used to print digital watermarks or to create matt-gloss effects. Multiple coating applications are used to reproduce structural effects of varying thickness, such as leather surfaces or tactile security marks on banknotes.
These articles may also interest you:
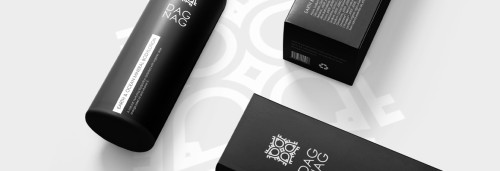
Cosmetic packaging
When it comes to cosmetics packaging, the first impression often decides whether a purchase is made or not. Due to the saturated market, manufacturers are forced to present their cosmetic products in ever new packaging designs.
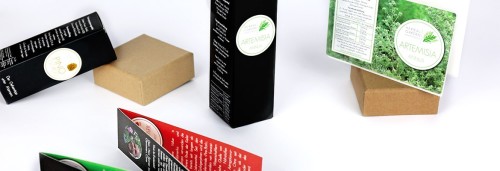
Beautiful boxes in corporate design
If a company wants to be more than its products and services and convey a positive and memorable brand feeling, a well thought-out corporate identity is necessary.
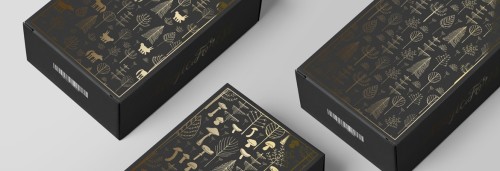
Black cardboard: noble material for special purposes
At first glance, folding cartons serve only one purpose: to package various products. Our range of materials for folding cartons includes different cartons in various thicknesses and basis weights.