Tubes are made of different materials. Each material has specific properties, advantages and disadvantages. In order to decide on the optimum tube material, the subsequent intended use and the properties of the respective filling material are the decisive factors. The variety of material types enables customized and resource-saving packaging solutions for every application.
Of the 15.5 billion tubes produced by European tube manufacturers in 2018, 38% were made of laminate, 35% of aluminum and 27% of plastic. Especially in the field of packaging for organic products and natural cosmetics, there are tubes made of alternative materials. These are made of wood fibers, bamboo or cardboard. Their share of the total volume is far below one percent.
All important tube types at a glance:
- Plastic tubes
- Laminate tubes
- Aluminum tubes
THE PLASTIC TUBES
This type of tube includes monolayer tubes, seamless coextruded tubes and laminate tubes.
Markets: Plastics are increasingly replacing aluminum in tube production. Aluminum is energy-intensive in production and the unit costs per tube are more favorable when using plastics. The tube bodies of plastic tubes are mainly made of polyethylene (PE) and polypropylene (PP), and the closure is made of polypropylene.
All types of plastic tubes are ideal fillable tube packaging for fast moving consumer goods (FMCG). FMCGs are consumer goods that consumers buy frequently and usually need on a daily basis. FMCGs turn over quickly at retail. These include food, cleaning products, detergents, hygiene and personal care products. Consumers buy these items spontaneously and routinely without a long decision-making phase.
Barrier: Tubes made of plastic have different barrier properties. The range extends from high-barrier properties to lower barrier behavior. Not all of them require high barrier properties, since the filling materials they contain are often subject to rapid consumption or there are few mass transfers.
Convenience: Plastic tubes allow simple, economical and hygienically clean dispensing. The fillable plastic tube springs back elastically after removal; there is a slight reabsorption of filling material or air during dispensing. Depending on the thickness of the material and the closure, this effect can be reduced. The plastic tube can have different closure variants.
Sustainability: Tube manufacturers see the issue of sustainability as an important driver and influencing factor for the development of packaging. Plastic tubes are recyclable. Germans collect them in the yellow bag or yellow garbage can. Waste management companies take the plastic waste to sorting plants. There, the different types of plastic are separated, and empty PE and PP tubes go for recycling.
The discussion about the increasing pollution of the oceans by plastics and plastic waste has resulted in numerous brand manufacturers and retail chains entering into far-reaching voluntary commitments. According to these, only recyclable or reusable packaging is to be used from 2025. The environment is also close to Labelprint24's heart, which is why recyclable PP tubes are now part of the product range.
Attractiveness: Consumers buy an attractively packaged product that appeals to them both visually and haptically. The printed plastic tube is a real eye-catcher at the point of sale and offers high differentiation from competitor products. This is an important feature both for the brand owner, who wants his product to stand out from the competition, and for the consumer, who has to make a purchase decision at the supermarket shelf.
The most important advantages at a glance:
- favorable manufacturing costs
- graduated barrier properties
- wide range of materials
- ideal packaging for FMCGs
- simple, economical and hygienically clean dosing
- Recycling possible
- good printability
PRODUCTION OF PLASTIC TUBES
Plastic tubes are produced by tube manufacturers using the extrusion process or the coextrusion process. During extrusion, plastic granulate (the extrudate) is melted and homogenized in an extruder by friction and heat input. After the plastic exits the die on the extruder, it solidifies by means of water cooling. The application of a vacuum causes the profile to adhere to the outer wall of the calibration, and the molding process is complete.
If two or more materials of the same or different types are brought together before leaving the profile die, this is called coextrusion. In the course of extrusion or coextrusion, tubes can be produced in almost any length. The "endless" plastic tube is then cut to tube length by rotary knives. The tube shoulder with the tube thread is formed, the resulting tube body is printed with the motif, possibly with additional finishing, and the tube cap is attached.
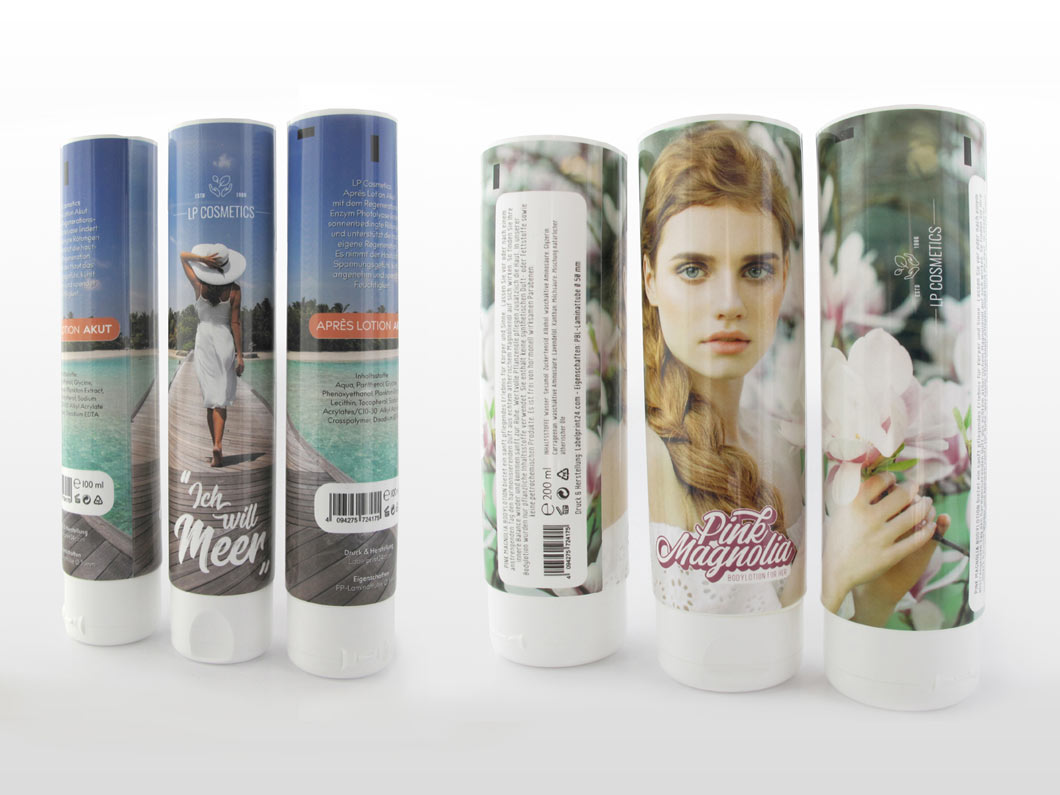