Chromo board:
Chromo board is a multi-layer board made of waste paper or wood dust with a coated, flat surface. In general, chromo board has a very high strength for paper material and is often used instead of corrugated board, solid board, or other fine carton. Plastic boxes are less affordable, have a higher environmental impact, and are more difficult to recycle.
How folding cartons are manufactured
There are several steps in the process of manufacturing printed folding cartons. The number varies for each job and depends on the carton's intended purpose, the amount of finishing, and additional processing steps.
Making a box foldable
Basically, all folding cartons must be punched, with grooves, fold lines, and notched. To ensure that the folding carton can be readily folded, the printed sheet must be scored with fold lines. These are pressed into the material so that the carton can later be folded over without tearing.
Scribing the carton
The outside of the board is scribed, partly cut without going all the way through, to allow flaps or openings to be punched out later by the customer. Finally, the punched carton blanks are broken out and fed into a folding carton gluing machine.
Punching contours
The printed and finished sheets are then fed into a flatbed die cutter. The contours of the carton are punched out with the aid of a punching die made of a razor-sharp material, usually a finely honed steel strip. By pressing the sharp-edged punching tool into the board, the paper fibres are cleanly separated from each other. In general, paper, carton, and corrugated board can be punched. When producing a generic folding carton (without imprint), punching is the first processing step. The right cutting die for every folding carton can always be ordered to measure in our folding carton calculator from labelprint24.
Gluing and shipping of boxes
Since the majority of the folding cartons produced have to be assembled with an insert or auto bottom in machine packaging systems, it is necessary that they can be opened precisely, reliably and easily. First, the creases are made soft and supple. In the final step, the punched-out box blanks are glued at points along the longitudinal seam or on the side parts. The finished folding cartons are then folded and sent to the customer.
Production process from order acceptance to dispatch to the customer
1.1 The pre-print stage
Before printing, the customer data is used to prepare the print data for the respective printing system, colours are selected, and the printing plates required for conventional printing are produced. If the order is processed using digital printing, a PDF print file is required. The cutting dies required for the cutting process are also ordered or created at this stage.
1.2 The actual printing process
If all the necessary materials are in stock, the production of the folding cartons usually begins with the printing. If the folding cartons are printed using offset printing, the paperboard must first be cut to the format that fits the offset printing machine. The offset printing machine is set up with the printing plates and the inking units are filled with the inks chosen earlier. After the first few cartons are printed, the printer compares the result with the proof. If approved, the print job is carried out. During the process, the printer continuously monitors the print image and readjusts the machine if necessary.
With digital printing, the boxes are not printed as sheets but instead as rolls. This means that the print motif is printed repeatedly on a paperboard roll. There is no need to create printing plates. After the digital printing process is complete, the printed paperboard is rolled up again. Other printing processes used for carton printing include flexo, screen, and intaglio printing.
1.3 Digital printing of cartons
An important taself-adhesive for packaging is to create positive customer experiences. The packaging can be the decisive factor and might even include personal messages. Digital printing technologies and the associated flexibility in production enable a very high degree of individualisation and personalisation. Printing a single carton is no longer a rarity. Carton manufacturers will use fast and cost-effective digital printing, especially for small print runs, ranging from 1 to 15,000 copies. This also allows them to offer quick turnaround, too.
Affordable custom cartons: digital printing makes it possible
Digital printing of made-to-measure folding cartons is not limited to the actual printing process, but also includes the ordering process and digital further processing and finishing. Digital is related to the word "digit" and involves binary, machine-readable data. The entire digital production process of folding cartons and shipping boxes is based on the processing of data. This print data can be read directly by computers using software, processed, then passed on to other devices in the production process, such as a KAMA or laser punch.
This type of data processing offers enormous time and cost advantages for the production of folding cartons since printing plates and mechanical cutting dies are no longer required. Carton costs are generally influenced by a number of factors: the print run, the dimensions, the printing involved, the material, and the construction. All of these factors can be adjusted to allow for bespoke packaging for each and every product that needs to be packaged.
1.4 Offset printing of boxes
Offset printing is used for larger runs, usually starting at 1,500 pieces. A wider range of boards, colours, and finishes are available with offset printing. Offset printing is used for very high-quality packaging, mainly made of fine and ultra-fine corrugated board (E-, F- or N-flute) or paperboard. It is a sophisticated process offering the best results for medium-sized and large print runs of high-quality packaging.
1.5 Flexographic printing
Flexographic printing is a high-pressure process frequently used in the corrugated board industry. In a process similar to a woodcut, the plate is a relief and the areas that get printed are higher than those that do not. These are inked with printing ink and transferred directly onto the corrugated board. In flexo printing, the printing plates are usually made of photopolymer or rubber. The printing inks are transferred via rollers to the plate cylinders via a pressure pump or fountain roller. Flexographic printing is particularly versatile and is considered a high-quality printing process.
How does flexographic printing work?
Like offset printing and intaglio printing, flexographic printing is done on a rolling press and has its origins in the letterpress printing used for books. It is used for many materials and is often the last resort when other printing processes can't be used. In flexo printing, the printing elements stand out from the printing plate; this is in contrast to intaglio printing.
The inks used for flexo printing are mostly environmentally friendly, thin liquids. Depending on the materials being printed, different low-viscosity inks are used. The printing inks are either UV-curing, water-based, or solvent-based inks.
The flexo printing machine
A modern flexographic printing press has an average of four to ten printing units. The production capacity depends on the arrangement of the printing units. A printing unit consists of an anilox roller, a plate cylinder, and an impression cylinder. The ink is transferred to the plate cylinder by the anilox roller. The motif is then printed on the impression cylinder, which guides the material through the unit.
What kinds of things are printed with flexographic printing?
Flexographic printing can be used on a wide variety of materials, including plastic, paper, and paperboard. For non-absorbent plastic films made of PP, PE, PVC and PET, the surfaces are treated to improve ink adhesion. Plastic packaging, adhesive tapes and films, and insulating paper are also printed using the flexographic printing process.
1.6 Screen printing
Screen printing is an all-round talent among printing processes. Almost all the printed T-shirts in the world are still screen printed. It has become an industry standard for professional and extremely durable results. Screen printing can also be used to print multi-colour motifs, colour gradients, special effect colours such as neon, gold, or silver, or even photos. The print is very thin, leaving only a slightly rubberised surface. Almost all textiles can be printed. Screen printing is particularly suitable for large print runs because it is very inexpensive, yet delivers the best results.
How does screen printing work?
The ink is transferred directly to the textile via a screen. Screen printing consists of an overlay, a frame covered with a mesh. A stencil is usually applied photographically to the mesh The stencil protect those areas not receiving the ink. In a printing machine, the overlay with the mesh is fixed over the fabric being printed. The printing ink is now applied to the fabric with a rubber squeegee, in which the open areas of the stencil are brushed or squeegeed onto the fabric. The ink is applied to the fabric by pressing it through the mesh of the overlay. As soon as the colour has been transferred to the textile, it is dried in a drying channel. In order to achieve good coverage and bright colours with dark textiles, they must first be printed in all white. The high wash resistance and excellent colour brilliance are some advantages of screen printing. Screen printing uses pigment and plastisol inks. Plastisol inks are characterised by their resistance to washing up to 60° C and their very long life. The plastisol ink can even be made boil-proof with special hardeners.
The fineness of the mesh is selected depending on the properties of the fabric being printed, the detail in the print motif, the size of the ink pigments, and the desired ink application. In screen printing, there is no standard mesh. Its fineness is measured either in grids per inch or threads per centimetre.
What kinds of things are printed with screen printing?
Screen printing is particularly suitable for large print runs for companies, clubs, events, sports events, workwear, etc., since a screen must be created for each colour of ink and this would otherwise be too expensive. This printing process is primarily used for T-shirts and sweatshirts.
1.7 Intaglio printing
Intaglio printing is one of the oldest printing processes still in use today. Even in comparison with ultra-modern digital printing, the intaglio printing process convinces with high print quality, uniform ink application, and rich, saturated colours.
How does intaglio printing work?
Intaglio printing is the opposite of relief printing processes like flexographic printing, since the areas to be printed are slightly incised onto a metal plate. These lines are created with the help of engraving, etching, or, nowadays, lasers. After the ink has been applied to the entire surface, a squeegee removes the ink from the non-recessed areas. The ink, which remains in the recessed areas, is transferred directly to the object to be printed with a contact pressure (consisting of two cylinders: the plate cylinder and the imprint cylinder). Intaglio is therefore a direct printing process. Only one colour is applied during each run. Modern machines must have good exhaust and fire extinguishing systems, since the inks used in this process contain a high proportion of easily flammable solvents. After the printing process, the printed surface moves to the next process or directly to the folding machine for further processing. The rotogravure and sheet-fed processes are used in intaglio printing. Rotogravure printing is mainly used to produce large print runs. A rotogravure printer can handle up to 60,000 prints per hour, which equals 16 metres/second. Sheet-fed intgalio printing is less common nowadays. It is used for printing fluorescent inks, coatings, and metallic inks on finished offset-printed sheets.
What kinds of things are printed with intaglio printing?
Intaglio printing is particularly economical for very large print runs and page counts (approx. 100,000). Magazines and newspapers such as Stern and Spiegel or catalogues such as the Ikea catalogue are printed using this printing process. Packaging such as those in the cigarette industry, tetrapacks, plastic and metal film packaging, as well as textiles and stock certificates are also printed using this process.
Characteristics of intaglio printing
Intaglio print images are always recognisable by the sawtooth effect. These are small dots that look like pixels on closer inspection. The humidity and the deepening of the printing plates cause this. To counter this effect, absorbent paper is often used, but the sawtooth effect is still not completely eliminated. Intaglio printing, however, delivers rich colour results and even application of the ink.
1.8 Hybrid printing of boxes
Box printing is a technical process which may use several different printing processes in sequence. It can make sense to produce a large print run of cartons using offset printing and then personalise them with variable data in digital printing.
1.9 Letterpress printing of packaging
Using letterpress printing to print cartons has largely been replaced by offset printing. Nowadays, letterpress printing is mainly used for printing on the surface of cartons. The force inherent in letterpress printing, with the printing elements raised on the printing plate, produces characteristic creases. With soft, uncoated papers, this leaves behind an almost relief-like result. If you are looking for a haptic and visual experience for your cartons, though, letterpress printing would be your first choice.
1.10 Coatings
If the carton surface requires no further refinement, the printed sheets or rolls proceed directly to the grooving, creasing, scribing, and die-cutting stages.
The cold glues used for die-cut packaging adhere securely to the uncoated areas of the carton. For this reason, the areas to be glued should not be coated or laminated. Otherwise, they will have to be mechanically roughened before gluing.
If the customer wants an additional finish to the box's surface, further production steps are necessary. A popular form of finishing is full-surface or partial pressure coating. This process usually takes place directly after printing in an additional inking unit or in digital printing with an inline or adjacent finishing system and can be carried out in a single pass in glossy, satin, matte, or textured surface.
The simplest and oldest method of coating is to apply an oil-based coating under pressure. A coating is applied to the box not unlike a printing ink. The coating will then dry through oxidation. Quite a large variety of coatings are available. In offset printing, it is also possible to apply metallic coatings on all or some of the surface in the fountain units.
When pressure coating with UV coating, it cures in a fraction of a second as the liquid binder components are exposed to UV rays. UV coatings consist of polymerisable binder components and photoinitiators and are characterised by a particularly high gloss combined with high mechanical protection, also against chemical effects. In addition to digital printing, UV coatings are also used in web offset printing and screen printing. UV coating is not recommended for food packaging because it can emit odours.
Pressure coating with water-based dispersion coatings is a technique in which a water-based dispersion coating is applied via a dampening unit with textile-covered dampening rollers. The drying technology used is important. The dispersion coating is based on various polymer dispersions.
1.11 Print finishing
While the first printed cartons at the end of the 19th century featured a discreet black-and-white screened print image, cartonsnow get all sorts of refinements and finishes. On the one hand, there are of course functional reasons, such as barrier properties, which allow box manufacturers to dig deep into their bag of tricks, but the main reasons for this evolution lie mainly in the requirements of modern product marketing.
The raw material of the folding carton is printed in a sheet-fed offset printing machine. Any motif or colour is possible and either the entire or part of the surface can be printed. If desired, the printed sheet can then be finished in another printing unit with a high-gloss or silk-matte coating. These two operations are carried out in one operation.
1.12 Why are finishes so important?
In the past, it was the transport and protective functions of packaging that were key, since longer distances had to be covered. A carton with a lid had to be stable, stackable, and resistant to outside forces. As industrialisation progressed at the beginning of the 20th century, beautiful cartons were given additional tasks, such as convenience (dimensioning the products into sales units). At the same time, packaging increasingly came to be used to promote sales. This function only grew with the emergence of supermarkets, self-service, and branded goods. Packaging is now intended to attract buyers by catching their eye as they survey the wide range of goods on offer.
Since the 1990s, the requirements for packaging materials have again changed. As consumers' environmental awareness has grown, attention has turned to questions of disposal and recycling. More information has to be displayed on the cartons's surface and packaging that is easier for an ageing population to open and close has also become important. Folding boxes can only do justice to this variety of functions with product design and finishing opportunities.
1.13 Which finishes are available?
There are various options for refining packaging. In addition to coatings, finishes include laminating, protective laminates, hot foil stamping, cold foil stamping, blind stamping, etc.
1.13.1 Laminating
Lamination is a process in which the printed material (paper, cardboard, paperboard) is glued flat with a glossy, matt, transparent, or structured plastic film. This lamination with foil changes the appearance of the folding carton surface. It also protects the carton contents from dirt, moisture, abrasion, and chemicals. Film lamination is primarily used when products are to be protected for the long term and/or the customer wishes to enhance their appearance. Lamination makes folding cartons even more resistant than conventional UV coatings.
1.13.2 Protective laminate
A protective laminate is a transparent adhesive film that offers protection and refinement in one. The protective laminate offers the product a long service life because it protects the digital print against UV radiation and mechanical influences. But it is also used for finishing. A glossy laminate gives the printing inks a higher brilliance. A matte laminate prevents reflections on the surface of the print. Protective laminates are frequently used for vehicle lettering or adhesive films that are exposed to mechanical loads, high solar radiation, or strong weather conditions.
1.13.3 Hot foil stamping
In hot foil stamping, an embossing foil is transferred to the material with the aid of heat, pressure, exposure time, and an embossing die. The foil can create different motifs, surfaces, contours, and writing. This process also has no waiting times for drying and curing. There are different colour foils, but also structured and gold or silver foils to choose from. Due to its visual appeal, hot foil stamping is particularly suitable for folding cartons that are intended to convey a high-end look, for example, jewellery or cosmetic product packaging. Hot foil stamping has its origins in traditional blind embossing. This reshapes the material without applying any ink.
1.13.4 Cold foil stamping
Relatively new to packaging printing is cold foil embossing. By transferring an aluminium layer and a protective coating which are detached from a carrier foil, a wide variety of metal effects can be achieved. The cold foil adheres to the box via an adhesive layer pressed onto the surface. The optical effect of cold foils is similar to that of stamping foils. Iridescent and reflective surfaces, such as metal, water or glass, can be created. Starting from only one standard silver foil, almost any metallic colour can be produced by overprinting. Since cold foils are sensitive to mechanical stress, additional surface protection (dispersion or UV coating) or film lamination must be subsequently added.
1.13.5 Dispersion coating
Dispersion coating is used as a finish and also protects against yellowing. It also makes the print job resistant to stacking and rubbing. Finishes with dispersion coatings are mainly used for menus, business cards, packaging, flyers, brochures, etc. The dispersion coating is water-based and is applied inline via a coating unit in the offset printing press, achieving a matte to medium glossy look. The drying phase is very short due to the high water content, which evaporates quickly.
1.13.6 UV coating
UV coatings are cured using UV rays, making them much more complex to use than aqueous coatings. However, UV coatings can create thicker layers to make the box highly resistant to abrasion and give it a very high gloss. It is also possible to create textures with the coating to produce different haptic effects. A UV coating can also be used on only part of the package to highlight specific areas on the box.
1.13.7 Blind embossing
The most traditional and oldest variant of finish is blind embossing. Pressure is applied to the printed products, creating a sculptural deformation. By the way: blind embossing can be combined with most finishing techniques, in particular with foil lamination. It creates a colourless, but special feel that has a very refined, subtle effect.
1.13.8 Form punching
A specially manufactured punching die can be used to mechanically cut out any shape from a substrate. For example, certain pictorial elements or a window can be emphasized in this way. Because this technique requires a custom die, it is more common on higher print runs. The design must take the underlying surface and the cutting edge into account. Materials such as coated, uncoated, and long-fibre papers of all grammages, foils, metals, and carton are suitablefor die-cutting. Punching out part of the surface will, of course, cause it to lose some of its stability.
2. Folding carton types
There are as many different types folding cartons in use. Founded in 1960, the European Carton Makers Association (ECMA) published the ECMA Code, a collection of folding carton design styles. This code is used to describe almost every type of folding carton imaginable. The
ECMA code classification system for carton packaging distinguishes six categories of boxes:
- Rectangular folding carton with longitudinal seam gluing,
- Rectangular folding carton without longitudinal seam gluing,
- Folding carton not rectangular with longitudinal seam gluing,
- Folding carton not rectangular without longitudinal seam gluing,
- Folding carton with product integration and
- Other folding cartons
Below we present some of the most common types of folding cartons in more detail.
2.1 Folding cartons with tuck-in flap
.png)
The production of
folding cartons with tuck-in flaps begins with the printing of the paperboard sheets. The printed paperboard sheets can then be refined in a variety of ways. The most common finishes include embossing and perforating, laminating and coating, or adding other materials such as plastic or metal foils. After printing and finishing, the blanks are cut from the printed sheets and the folds are grooved. After it is punched out, the body of the carton is provided with adhesive dots at the adhesive flap and glued together. This type of bonding is called side seam or longitudinal seam gluing. Side seam gluing is done at high speed on an automatic gluing machine.
The carton surface can be printed with any colour motif on any outside or even inside wall. This extensive printing area can be used for advertising purposes or to provide information about the manufacturer, dosage, detailed ingredients, etc.
Folding cartons with tuck-in flaps are usually made of a solid paperboard. The solid board maintains the box shape when filled and protects the contents during transport and storage. Paperboard is easy to print, easy to fold and, above all, recyclable.
In the pharmaceuticals and medication industry, this printed folding carton is used almost exclusively as packaging for small doses of medicines or preparations. In order to pack such medication blisters (also push-through packs) in printed folding cartons with tuck-in flaps, the resealable lids of the boxes are usually provided with one or two lateral tuck-in flaps. Folding cartons with tuck-in flaps are often equipped with locking slots and dust protection. These keep dust and other foreign bodies from penetrating the interior of the carton. We specialise in printing folding cartons and can also produce small runs of individually designed folding cartons. All sides of the carton can be printed with individual motifs, graphics, logos, slogans, barcodes, QR codes, or other information.
All of the typical finishes for printed matter are also available. Print coatings and hot or cold foil stamping on the folding box are particularly popular, either to protect the packaging from external influences or to improve its feel and appearance. Folding boxes with tuck-in flaps are some of the most refined packaging materials available.
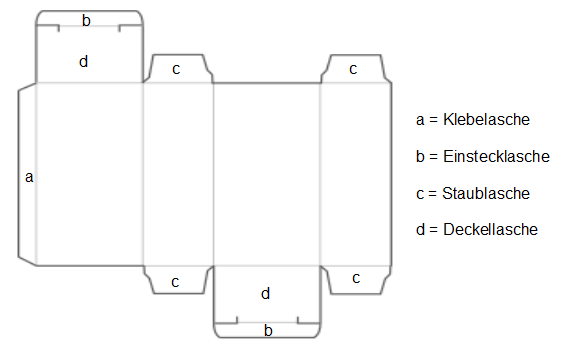
The folding carton with tuck-in flaps is the most widely used and inexpensive type of printed folding carton. On both its lid and base, it has two lateral dust flaps and a tuck-in flap that closes with friction. However, the flaps themselves do not provide a secure seal for the box. The tuck-in flap can also be equipped with locking slots or a closing tongue to guarantee a more secure hold on the lid. These boxes are often used for medicines, software, cosmetics, tubes of all kinds, and small bottles.
2.2 Folding cartons with reverse tuck end
.png)
In industrial packaging,
folding cartons with reverse tuck ends are mainly used to package products requiring a stable bottom due to their weight. The reverse tuck end prevents the contents from slipping downwards.
Typical applications include cases of glass bottles, secondary packaging, cosmetics in glass containers, colognes, ceramics, and beverage cans. Whenever a "normal" tuck-in flap does not close the base firmly enough and the product could slip through it, folding cartons with an reverse tuck end are the safer alternative. The packaged goods press down on the interlocking tuck-in flaps and thus strengthen the stability of the bottom. The reverse tuck end also ensures that the folding cartons are stable. Unlike auto-bottom boxes, boxes with reverse tuck ends do not automatically set up when filled.
All six sides offer space for information and advertising. The invisible parts of the reverse tuck end are cut away during printing.
The folding carton with reverse tuck end also fulfils several functions simultaneously for the product inside it. It protects the contents from external influences such as dust, moisture, light, or scratches. It serves as transport packaging and ensures that the products can be easily stacked and presented on the shelves. The surface can contain information and advertising or hold secondary packaging, such as labels. Folding cartons and their contents almost always form a product unit and consumers perceive them as such.
labelprint24 can offer plain folding carttons with reverse tuck ends or also print them with individual motifs and design. Just go online and use our calculator to place your order. Depending on the box's required strength, various grammages of carton are available. Of course, our chromo board folding carton is also great as as a give-away at trade fairs. Individual folding cartons for use in marketing can be filled with promotional items of all kinds (ballpoint pens, key rings, stickers, sweets, etc.). As experts in providing folding cartons for promotional purposes, we can offer any size imaginable.
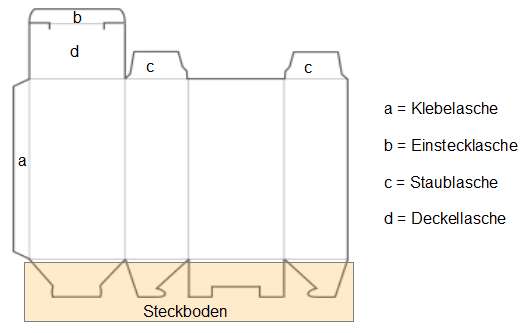
The folding carton with reverse tuck end is a special form of the box with tuck-in flaps. The reverse tuck end consists of one flap on each of the four sides of the bottom opening. When assembled, the flaps fold inwards and hook into each other. They lock each other in place and thus prevent the contents of the packaging from falling out.
2.3 Folding cartons with auto bottom
.png)
Folding cartons with automatic bottoms are another special form of cartons with tuck-in flaps. The auto bottom is glued during production and is therefore extremely stable. Filling these cartons is especially quick and easy, since the bottom automatically assembles when filled.
If the auto bottom has a glued longitudinal seam, the base closes automatically as the walls go upright. The folding carton straightens itself up. The auto bottom offers the advantage that the folding cartons can be quickly and reliably loaded with a product both manually and mechanically. With this type of box, the longitudinal seam is glued to one side before delivery; they are delivered flat.
2.4 Folding cartons with tuck-in flap and Euro slot hanger
.png)
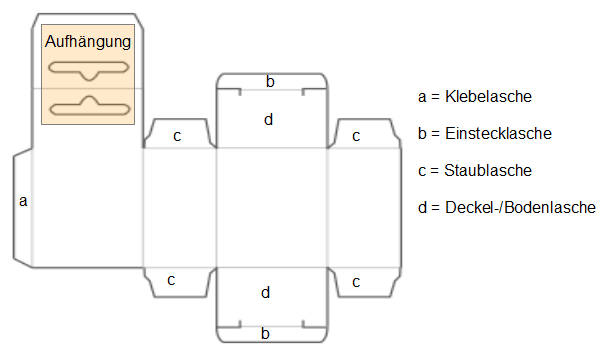
The
folding carton with tuck-in flap and Euro slot hanger has a stable additional tab in the lid with a punched out slot for hanging. This makes the boxes easy to display for self service at supermarkets, electronics stores, or DIY stores. Hanging boxes are typically used to package ink cartridges, metal goods, small electronic devices, or toys. The stability of the lid and bottom vary depending on the weight of the contents and can use tuck-in flaps, an auto bottom, or locking slots and tongues.
2.5 Pillow boxes
Pillow boxes with their eye-catching, curved shape are aesthetically pleasing while optimally protecting their contents. Pillow boxes are inexpensive to produce and easy to open and close again. Pillow boxes are ideal for packaging T-shirts, promotional items, giveaways, and gifts. Setting up a pillow box is particularly easy and very fast. The printed and unprinted pillow box can also be produced open on one side (without closure). This is popularly used for sandwiches, mini pizzas, burritos, etc.
Pillow boxes printed and unprinted in different carton thicknesses and and grammages:
Individually printed pillow boxes are primarily used to package promotional items and gifts, but they are also used in industry, for example, to package earplugs and the like. Due to their elegant convex design reminiscent of the shape of a pillow, printed pillow boxes may not be so easily stacked after filling, but they are particularly eye-catching to consumers. This effect is enhanced by the printing and finish.
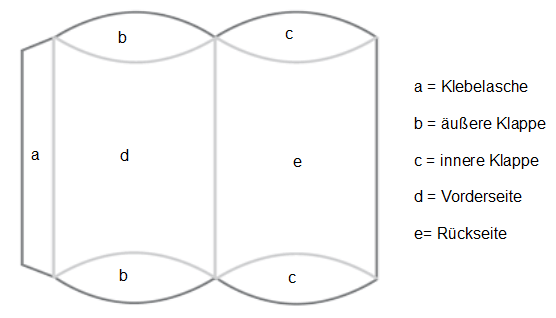
Choose an original, full-surface or matt print and a high-quality finish. We offer you low-cost chromo board (multi-layer board made of waste paper or groundwood with coated, flat surface) for perfect printing results. You can also select the width, height, and depth. We print your pillow boxes in offset flexo printing (CMYK) for rich colours and the best possible print quality. In contrast to conventional printed folding cartons, pillow boxes do not close with tuck-in flaps, but instead have foldable board flaps. These pillow boxes are easy to open and close again and are individually made with your desired motif to hold gifts or promotional items with your logo, slogan, and contact details. In order to guarantee the stability of this type of packaging, we manufacture your individually printed cushion boxes from a sturdy chromo carton. Use our online calculator to create your individual pillow box in the format and size you require for use as gift boxes, advertising material, or industrial packaging and order directly on from reliable printing professionals in business since 1950.
2.6 Folding carton with straight tuck end
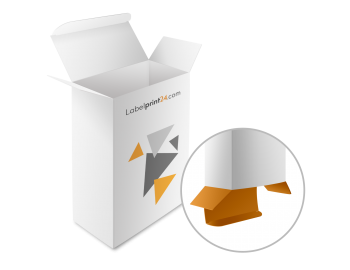
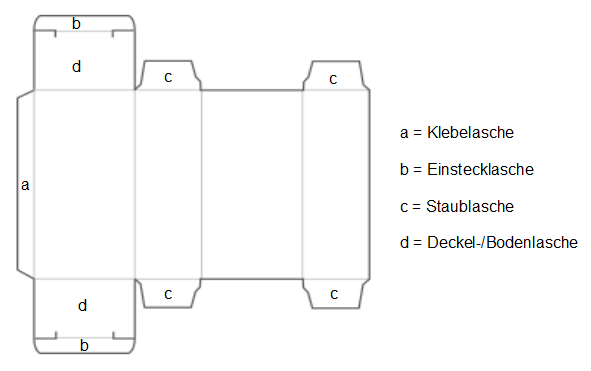
The
folding carton with straight tuck end is made from a single piece of board. The long side of the body is glued with the glue flap. The folding carton is securely closed by folding in two dust flaps and a tuck-in flap on both the top and bottom. Typical uses for this type of packaging include packaging for medicines, foodstuffs, computer accessories, or cosmetic products. It protects products from external influences such as dust, moisture, scratches, or light. This packaging is optimal for transport, stacking, and presentation of products.
2.7 Carton slipcase
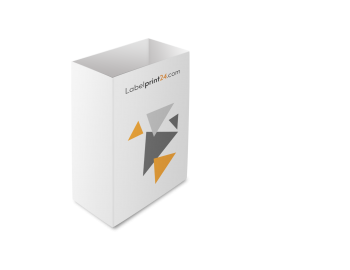
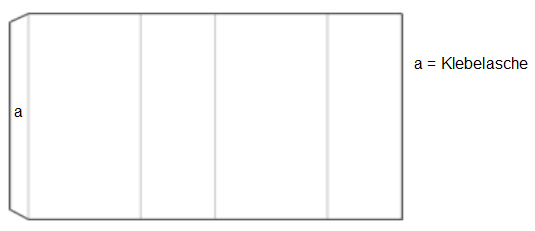
The
carton slipcase is an elegant and high-quality packaging solution that makes products look even more valuable and first-class. Due to its robustness, it not only offers a high-quality finish, but also stable protection for the product, which does not suffer any loss of quality when opened and closed multiple times. A slipcase is a carton container closed on four or five sides and open on one or both ends. The internal product is protected, but also given a special refining accent. The carton slipcase also provides a large area for advertising messages or information. The carton slipcase is often used as a classic book slipcase, as gift or advertising packaging, or simply as a cover for a DVD collection.
2.8 Dispenser box for labels
.png)
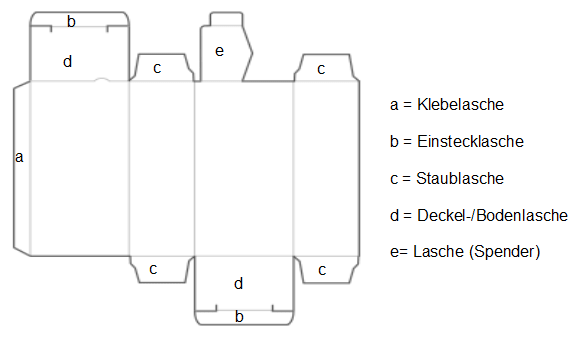
The
label dispenser box has flaps that can be tucked in. The roll labels are easy to insert into the dispenser box and can be removed individually by hand. The dispenser box safely stores the labels and protects them from soiling, buckling, or other damage. Due to the folding technique, it is possible to print messages on the dispenser box from all sides. A dispenser box protects roll labels and makes them easy to handle.
2.9 Boxes made to measure - FEFCO
Boxes can be made to measure according to the FEFCO standard. Despite their low weight, shipping boxes are extremely stable thanks to their construction. They offer protection against transport and storage damage. Custom-made carton boxes are mainly used for moving or as packaging for products, trade goods, etc.. For more information on made-to-measure boxes, click
here.
3. Cartons with slip-on lids & hinged-lid boxes
Folding cartons with slip-on lids have a particularly large lid opening. This makes them particularly suitable for shipping or storage of printed matter. They can readily be opened and closed several times. Boxes with slip-on lids are frequently used as packaging for high-quality products or as gift packaging. Opening the lid becomes an event in its own right, making the contents seem all the more special.
Like our
folding cartons , our boxes with tuck-in flaps are punched and glued from only one piece of board. Boxes with slip-on lids, by contrast, consist of two separately produced carton parts: the base and the lid. Both parts must still fit together after filling. The printed slip lid box is delivered flat and then assembled by hand. Slip-on lid boxes are often used to package high-end textiles, such as T-shirts, shirts, ties, or underwear. They are also typical packaging for chocolates, while other foodstuffs tend to be packaged in boxes with hinged lids. Unlike slip-on lids, hinged lids are connected to the base of the box. They are opened from above, not unlike a treasure chest. We have such chocolate boxes in our portfolio.
3.1 Two-piece sliding boxes (matchboxes)
Another variant of folding boxes made from two parts are two-piece sliding boxes, most commonly seen as matchboxes. The inner box is slid inside the outer box. Two-piece sliding boxes are often used for gifts, perfumes, cosmetics, pens, knives, ampoules, or, indeed, matches.
3.2 gable boxes
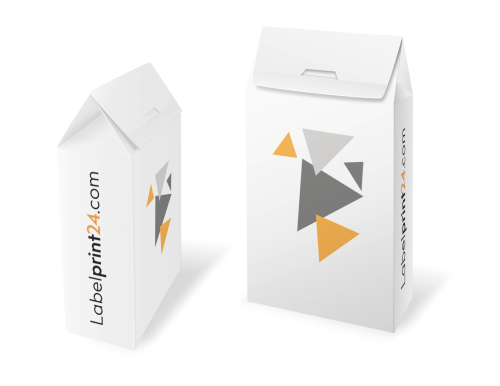
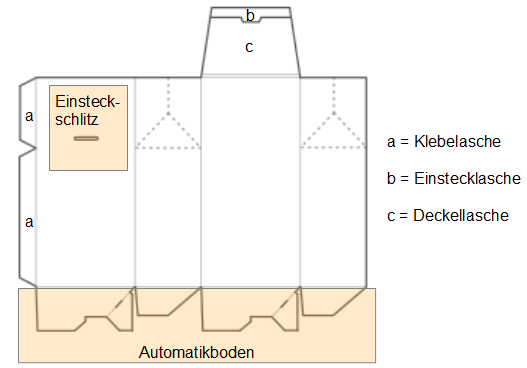
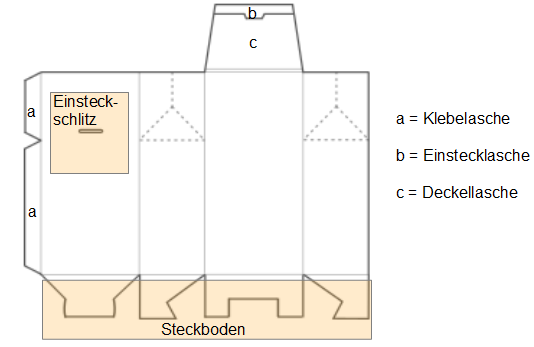
Gable boxes come in a number of different versions and are a refined variant of the classic folding box. Gable boxes are often used to package tea, coffee, spices, or herbs. But they are also ideal for use as packaging gifts, jewellery, confectionery, or giveaways, since they make what's inside seem all the more special. A punched out viewing window or carrying handle will add further to this messaging. A special refinement such as a dispersion coating or blind embossing can further enhance the advertising effectiveness, making the product inside appear even more exclusive and appealing.
Gable boxes with auto bottom are particularly stable and tear-resistant because they are glued. This makes them impermeable and prevents small products from slipping through. The gable box has a rectangular body with pointed, converging sides that form the gable. After filling to the base of the gable, the top is pressed together and closed by inserting the cover flap into the slot on the back. Gable boxes with crash lock bottom also offers a tight closure, but without adhesive. When the box is assembled, the four tabs interlock, making the box quick and easy to fill. The advantage of this variant is that it can also be filled from below.
3.3 Shipping packaging
Deutsche Post sends its greetings! Folding cartons for shipping or post boxes can be found in every parcel shop with prepaid postage and ready to seal with the enclosed adhesive strips. Sturdy, printed boxes made of thick carton or corrugated board are the ultimate shipping packaging and drive today's increasingly booming mail order business. Shipping boxes are delivered flat to save space. First the bottom and then the lid have to be assembled. Particularly stable folding boxes can be found in every DIY store and are perfect for moving house, since they are made of multi-layer corrugated board.
3.4 Hexagonal boxes
Who says folding cartons can only be rectangular? How about a hexagonal box? Sweets such as Duplos, olive oil, beverage bottles, or other round goods can be safely and effectively packed in such boxes. For heavy products, it is particularly important that the bases of the hexagonal boxes be load-bearing and stable and provided with adhesive dots.